IBEW Powers Up Massive Auto Plant Expansions
April 17, 2014
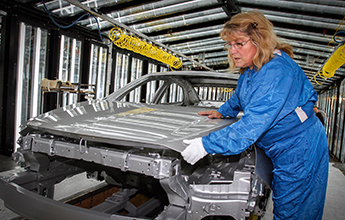 |
Members of Kansas City, Mo., Local 124 renovated GM’s factory in Fairfax, Kan., where thousands of UAW members build the Chevy Malibu, the Buick LaCrosse and the LaCrosse eAssist Hybrid. Photo used under a Creative Commons license from Wikimedia user General Motors .
|
Drive down any wide, open highway across Missouri and you’ll see something big, heavy and plentiful on the plains.
Pickup trucks. Lots of them.
The popular Ford F-150 truck gets around the nation, but it’s practically emblematic of the Heartland. And thanks to hundreds of IBEW electricians, the company’s $1.1 billion expansion of its sprawling factory just outside Kansas City, Mo., will keep the carmaker’s production line steady and reliable.
Which means jobs. Five thousand of them for local residents, members of the United Auto Workers, who build the trucks at the plant in the town of Claycomo in the northwest part of the state. But it also represents much-needed employment for hundreds of IBEW electricians on-site, hungry for a good day’s work after the worst recession in generations battered the construction industry.
Adding to Local 124’s good fortunes, General Motors mounted similar upgrades to its facilities across the state border in Fairfax, Kan. This meant even more work for journeymen and apprentices in the area – as well as travelers who helped man the jobs.
“It says a lot that some of the finest carmakers in the world want IBEW labor powering up their expansions,” said Local 124 Business Manager Terry Akins, who helped process more than 500 calls for electricians during the 2013 winter months at the height of both plants’ expansions:
It says even more that Ford is spending this money in Missouri, where we had been fighting a proposed right-to-work law. Ford’s huge investment flies in the face of anti-worker lawmakers who say that companies don’t want to do business in “right to bargain” states. This job is proof that major companies and collective bargaining can both thrive side-by-side.
Built Union Tough
At nearly 5 million square feet, Ford’s Claycomo facility produces more cars than any other plant in the U.S. The two-square-mile structure is a field of dreams for truck lovers. Raw ingredients like sheet metal, aluminum, glass and rubber wind through a network of conveyor belts and robotic assembly arms. Here, thousands of UAW members build the F-150, the industry’s top-selling pickup and Ford’s most profitable line.
The company is also “re-shoring” one of its more commercially-used vehicles, the Ford Transit. The tall, boxy-looking van boasts features suited for mobile businesses like contracting and delivery services. Formerly built in Romania, this year’s North American models are crafted at the Claycomo plant by a UAW staff with more than 1,000 new hires.
Local 124 journeyman wireman Jim Kelly served as field superintendent for his crew from Mark One Construction, one of several signatory contractors that manned the job to help get the F-150 and Transit lines moving.
“I’ve done car plants for nearly 40 years now,” said Kelly, a veteran hand who is native to the Kansas City area.
One of Kelly’s biggest jobs was to help install and power up all materials for the facility’s new stamping plant. That’s where all the fenders, hoods, and other body parts for the Transit get pressed and primed for assembly.
“That alone was more than a $6 million job,” Kelly said. In his years working in and around plants, he’s seen tasks evolve from working with heavy, rigid pipe – “very labor-intense,” he said – to focusing more on installing and troubleshooting the robotic arms that bob and weave to put the pieces of automotive machinery together.
The IBEW crew also built the $3.5-million conveyor system that ushers vehicles though the painting facility. On new F-150 and Transit models, Ford is using a new water-based paint and drying process that Kelly said is more environmentally friendly. That’s another “green” component to the new F-150, which is now built to be hundreds of pounds lighter to improve fuel efficiency.
Coming back from a previously sluggish employment outlook, “This job is a great boost to the local economy and it’s put our members back to work,” Kelly said.
Local 124 Business Manager Akins confirmed that. “These projects have brought us back to pre-recession levels of employment,” he said. “And continued upgrades will mean that we keep many members employed at the plants down the line.”
The enduring popularity of the F-150 prompted Ford management to boost production of the 2015 model. "We added a shift last year,” Ford Chief Operation Officer Mark Fields told KSHB Kansas City Channel 41. “We added 900 jobs to the third shift to produce our current F-series, and the investment we've made in the plant, both for the Transit and for this F-series, bodes really well for the area and the community.”
Akins marvels at the news. “That’s means they’ll be producing about one truck per minute,” he said. “And our members are helping make this happen.”
That also means Ford may soon have some repeat IBEW customers. “Three of Local 124’s agents drive F-150s,” Akins said. “It’s one of the best on the road.”
‘A Smooth Job’ at GM Plant
West of the state border at the General Motors plant in Fairfax, Kan., 3,900 UAW members build popular lines like the Chevy Malibu, the Buick LaCrosse and the offshoot LaCrosse eAssist Hybrid.
Like the Ford plant, GM’s facility spans several million square feet. And GM’s management has pumped more than $600 million into its historic facility, originally designed for construction of B-25 bombers during World War II.
Hundreds of journeymen, apprentices and travelers who worked at Ford also spent the winter building GM’s new paint shop and stamping press, where coils of sheet metal are molded into hoods, doors and trunks lids.
The size and scope of both the plant upgrades brought hundreds of travelers from as far as Washington, D.C., to help man the projects.
Twenty-three-year member Paul Lamb came from Nashville, Tenn., Local 429 to lend his tools and expertise to upgrading the welding portion of the GM facility.
“A lot of it was building up the conveyor systems,” Lamb said. After Lamb and other electricians ran conduit and pulled wire to power the systems, unfinished cars could begin automatically moving through various stages of the assembly process.
“It was a smooth job – I was there for 15 days, made some good money and had a nice time on the road,” said the 42-year-old, who has helped build steel processing centers, massive computer data storage facilities and solar farms. “It was a nice Band-Aid to get me through to the next job.”
With various building trades members represented on the projects at peak time, Akins said the IBEW’s stake will continue when the current ebbs. “Local 124’s part of the work is ongoing. There was a big ramp-up over Christmas when we sent hundreds of wiremen in there, and there are still many hands on the jobs.”
GM’s investment comes after a long rescue of the struggling automaker, which was freed from government ownership late last year. In the end, the investment worked: hundreds of thousands of union workers were able to save their pensions, and GM recently hit a record-high stock price. “The automaker’s shares soared 42 percent [in 2013], outpacing the 27 percent gain of the Standard & Poor’s 500 Index,” Bloomberg News reported in December.
The IBEW Business Advantage
The Ford and GM plant upgrades presented a mutual solution to two problems – the companies needed new infrastructure, and local IBEW electricians needed work.
But none of that would have coalesced without the skill and management of signatory contractors who employ IBEW journeymen and apprentices in the Kansas City area.
The largest signatory contractor on the projects was Electrical Corporation of America, which was processing in excess of $1 million in payroll checks each week of the job.
Company President and CEO Don Laffoon is a Local 124 member. “He went through the apprenticeship here, turned out, worked in the field and eventually bought the company,” Akins said.
It’s a similar story at signatory contractor Miller Electric, whose president, David Miller, also logged time as a Local 124 journeyman.
“It’s exciting to see,” Akins said. “We’ve grown people through our own ranks and watched them go even further in the business community. That keeps our members working and their companies successful.”
Electrical Corporation of America’s strong relationship with Kansas City-based UMB bank is critical not only to ensuring that the company flourishes, but that massive projects like the car plant renovations can be manned with IBEW labor.
“There aren’t too many contractors who can bankroll projects like these,” Akins said. “When it comes to making payroll, UMB knows that the money will be covered. ECA is one of their best customers. How many lenders can you go to and say, ‘I’m paying $4 million in payroll in the next three weeks,’ and the bank knows you’re good for it?”
Partnerships like that help signatory contractors attract high-dollar customers, rather than ceding jobs to the nonunion sector, Akins said.
Building Cars – And the Middle Class
For the greater Kansas City area, the success of the Ford and GM plants is paramount to maintaining good middle-class jobs.
United Auto Workers members at the Ford plant were thrown a curve ball when the company announced a few years ago that it was moving its production line of the popular Escape, a small sport utility vehicle, to Louisville, Ky.
Despite that blow to the local economy, the successful involvement of local politicians like IBEW-supported Democratic Gov. Jay Nixon has brought tax subsidies to both carmakers to keep other good-paying jobs rolling along at a steady clip.
In addition to the 900 Ford workers hired for the third shift to build the F-150, GM’s new paint shop will help ensure steady employment for UAW members and the IBEW electricians who will perform periodic upgrades.
"The employees at the Fairfax plant are dedicated to ensuring they build the highest-quality vehicles for our customers, and are looking forward to working in one of the most advanced facilities GM operates,” UAW Local 31 President George Ruiz said in a joint press release with the company. “All of our employees are pleased to know we will be working in Kansas City for years to come.”
Continued production is equally sweet for Ford employees. CNN reported in January that the carmaker will pay its union workforce about $414 million in bonuses after workers and management negotiated more generous profit sharing in their last round of collective bargaining talks. With Ford’s 2013 net income the strongest it had been in a decade, that means about 47,000 rank-and-file workers will get checks of nearly $9,000 each.
A constellation of factors – bolstered manufacturing, the rebound of the auto industry and continued popularity of American-made cars – held special resonance for IBEW electricians working on the plant upgrades.
“We’re losing our manufacturing every day,” said Paul Lamb, the traveler from Nashville. “Projects like this are good for the economy and show we can bring something back.”
Kelley, the Local 124 journeyman, agreed. “It’s also always good to know that you’re doing a job 100 percent union, and that the people who are working in this plant are our fellow union members too.”
Related News
Winning Back the Work: Buckeye State IBEW on Road to Recovery
Right-to-Work-for-Less Fails in Mo.
Apprenticeship 2.0: Games and Social Media Transform Apprentice Training

|